Understanding What is Porosity in Welding: Causes and Solutions
Understanding What is Porosity in Welding: Causes and Solutions
Blog Article
Porosity in Welding: Identifying Common Issues and Implementing Finest Practices for Avoidance
Porosity in welding is a pervasive problem that usually goes undetected until it creates substantial problems with the stability of welds. This usual defect can jeopardize the toughness and resilience of bonded frameworks, presenting security dangers and resulting in expensive rework. By comprehending the root causes of porosity and implementing effective avoidance approaches, welders can substantially boost the quality and reliability of their welds. In this discussion, we will certainly check out the essential elements adding to porosity development, analyze its destructive effects on weld performance, and discuss the very best techniques that can be embraced to reduce porosity occurrence in welding procedures.
Usual Sources Of Porosity
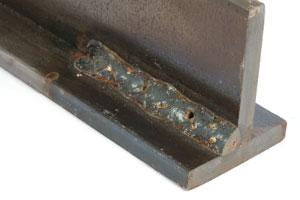
Making use of dirty or damp filler products can introduce pollutants right into the weld, contributing to porosity problems. To minimize these common reasons of porosity, detailed cleaning of base steels, correct shielding gas choice, and adherence to optimum welding parameters are necessary techniques in achieving high-grade, porosity-free welds.
Influence of Porosity on Weld Top Quality

The visibility of porosity in welding can substantially jeopardize the structural stability and mechanical homes of welded joints. Porosity creates voids within the weld steel, compromising its total toughness and load-bearing ability. These gaps function as anxiety concentration factors, making the weld much more vulnerable to fracturing and failure under used lots. Furthermore, porosity can decrease the weld's resistance to corrosion and various other environmental factors, better decreasing its longevity and efficiency.
Welds with high porosity levels tend to show lower influence stamina and reduced capability to deform plastically before fracturing. Porosity can restrain the weld's capability to properly transmit pressures, leading to early weld failure and prospective security hazards in important structures.
Finest Practices for Porosity Avoidance
To boost the structural stability and try this web-site top quality of welded joints, what certain actions can be executed to lessen the occurrence of porosity during the welding procedure? Porosity prevention in welding is vital to ensure the stability and toughness of the last weld. One reliable practice appertains cleaning of the base steel, eliminating any type of pollutants such as corrosion, oil, paint, or dampness that could cause gas entrapment. Ensuring that the welding tools is in great problem, with clean consumables and ideal gas circulation rates, can also considerably lower porosity. Additionally, maintaining a secure arc and regulating the welding specifications, such as voltage, current, and travel speed, assists create a consistent weld swimming pool that reduces the threat of gas entrapment. Utilizing the right welding technique for the specific material being welded, such as adjusting the welding angle and gun setting, can further avoid porosity. Regular examination of welds and instant remediation of any type of problems determined find out here during the welding procedure are essential practices to stop porosity and produce top quality welds.
Value of Proper Welding Strategies
Applying correct welding techniques is paramount in ensuring the architectural stability and top quality of welded joints, building upon the structure of effective porosity prevention actions. Excessive warm can lead to raised porosity due to the entrapment of gases in the weld pool. Furthermore, making use of the appropriate welding specifications, such as voltage, existing, and take a trip speed, is vital for attaining sound welds with marginal porosity.
Furthermore, the option of welding procedure, whether it be MIG, TIG, or stick welding, need to straighten with the details requirements of the project to make sure optimum outcomes. Proper cleaning and prep work of the base steel, along with selecting the best filler material, are likewise necessary parts of competent welding methods. By adhering to these best techniques, welders can lessen the risk of porosity development and create high-grade, structurally audio welds.
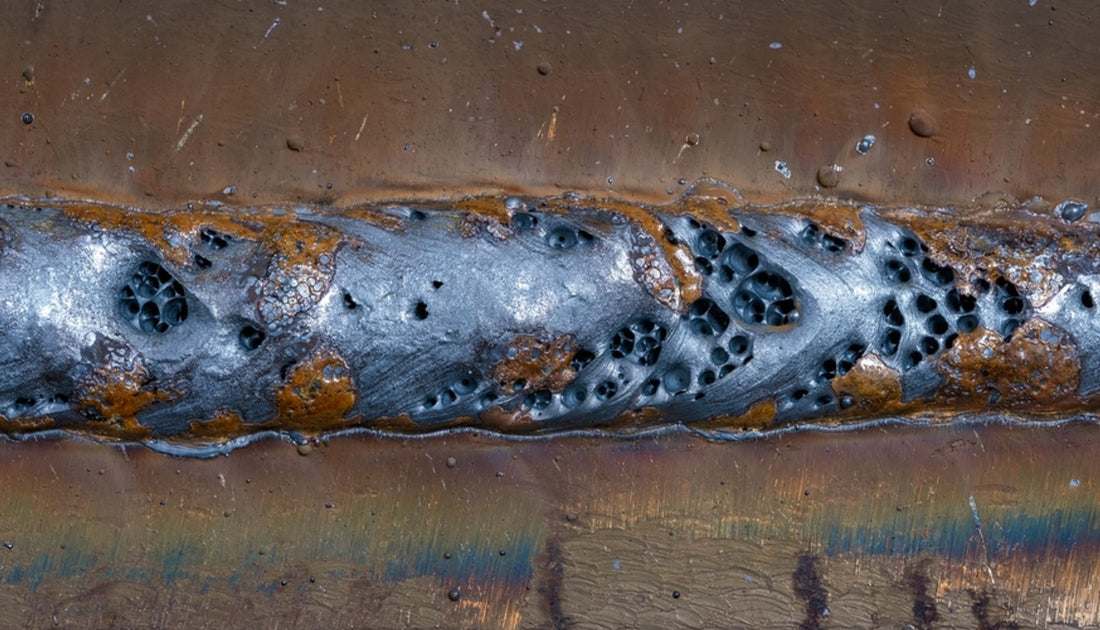
Examining and Quality Control Steps
Quality control procedures play an important duty in confirming the honesty and integrity of bonded joints. Testing procedures are vital to spot and avoid porosity in welding, making sure the stamina and longevity of the end product. Non-destructive screening approaches such as ultrasonic screening, radiographic testing, and visual inspection are commonly employed to determine prospective problems like porosity. These methods enable the assessment of weld quality without compromising the integrity of the joint. What is Porosity.
Conducting pre-weld and post-weld examinations is likewise crucial in preserving quality assurance standards. Pre-weld assessments involve validating the materials, tools settings, and sanitation of the work location to stop contamination. Post-weld inspections, on the other hand, assess the final weld for any kind of problems, consisting of porosity, and verify that it fulfills specified criteria. Implementing a detailed quality assurance strategy that consists of extensive screening procedures and assessments is paramount to decreasing porosity concerns and guaranteeing the general top quality of welded joints.
Final Thought
In final thought, porosity in welding can be a typical concern that influences the quality of welds. By identifying the typical reasons for porosity and carrying out ideal techniques for prevention, such as correct welding methods and screening steps, welders can make sure top quality and trusted welds. It is necessary to prioritize avoidance methods read more to lessen the occurrence of porosity and preserve the honesty of bonded frameworks.
Report this page